Gibson is the contract engine supplier of the P2 prototype machines in the FIA World endurance as well as many other championships. Besides the FIA, they are also providing LMP1-teams with an all new performance engine wit. With the help of Motul’s finest lubrication their engines are pushed to its absolute limit, race after race. We talked to technical director Ian Lovett and discovered the required ingredients needed to build a reliable endurance engine.
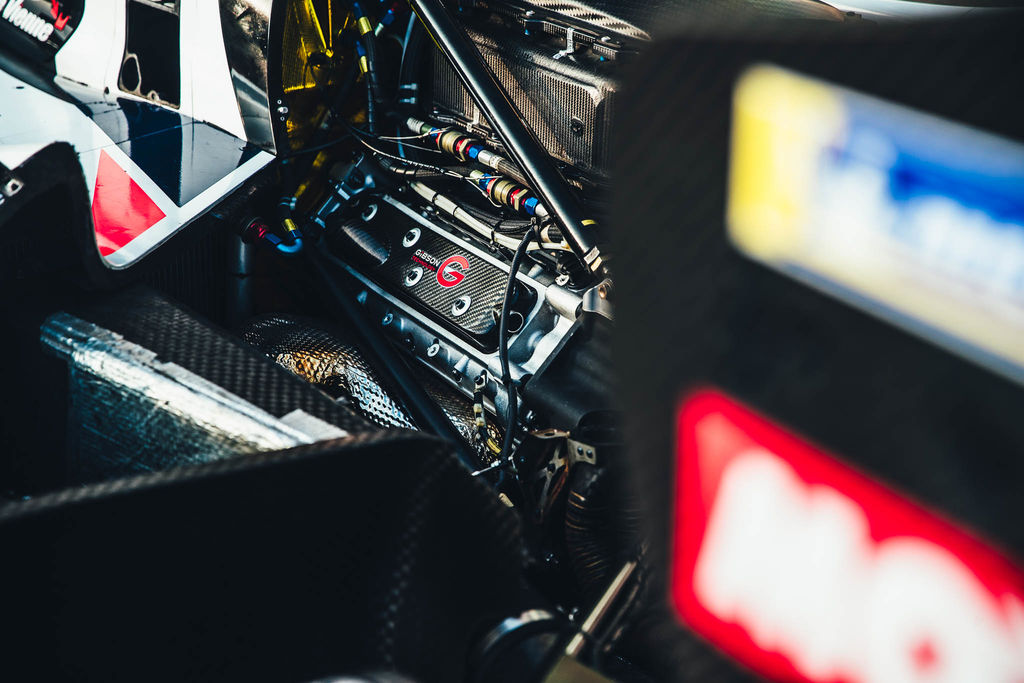